What is Porosity in Welding: Ideal Practices for Avoiding Permeable Welds
Wiki Article
Recognizing Porosity in Welding: Exploring Reasons, Impacts, and Avoidance Methods
Porosity in welding is a consistent challenge that can dramatically affect the top quality and stability of welds. As professionals in the welding sector are well mindful, comprehending the causes, results, and prevention techniques connected to porosity is vital for achieving durable and trustworthy welds. By diving right into the root creates of porosity, examining its detrimental results on weld high quality, and discovering effective avoidance approaches, welders can improve their knowledge and abilities to generate top quality welds continually. The complex interaction of aspects contributing to porosity requires an extensive understanding and an aggressive strategy to make certain successful welding outcomes.Typical Reasons For Porosity
Contamination, in the kind of dirt, grease, or rust on the welding surface area, creates gas pockets when heated, leading to porosity in the weld. Incorrect shielding takes place when the securing gas, frequently utilized in procedures like MIG and TIG welding, is unable to totally safeguard the molten weld swimming pool from reacting with the bordering air, resulting in gas entrapment and succeeding porosity. Additionally, poor gas insurance coverage, usually due to incorrect circulation prices or nozzle positioning, can leave components of the weld unprotected, enabling porosity to create.Results on Weld Quality
The existence of porosity in a weld can dramatically jeopardize the overall quality and integrity of the welded joint. Porosity within a weld produces spaces or tooth cavities that deteriorate the structure, making it extra at risk to fracturing, rust, and mechanical failure.Additionally, porosity can hinder the efficiency of non-destructive screening (NDT) methods, making it testing to spot various other defects or suspensions within the weld. This can cause considerable safety issues, specifically in critical applications where the structural integrity of the bonded elements is critical.

Prevention Techniques Overview
Given the damaging impact of porosity on weld high quality, reliable avoidance methods are crucial to maintaining the structural honesty of bonded joints. In addition, selecting the proper welding criteria, such as voltage, current, and take a trip speed, can aid minimize the danger of porosity formation. By incorporating these prevention strategies my sources into welding methods, the incident of porosity can be significantly reduced, leading visit homepage to stronger and extra trusted bonded joints.Relevance of Appropriate Shielding
Proper securing in welding plays a crucial role in protecting against climatic contamination and making sure the honesty of welded joints. Shielding gases, such as argon, helium, or a mix of both, are commonly used to secure the weld swimming pool from reacting with components in the air like oxygen and nitrogen. When these reactive components enter into call with the warm weld swimming pool, they can create porosity, leading to weak welds with decreased mechanical homes.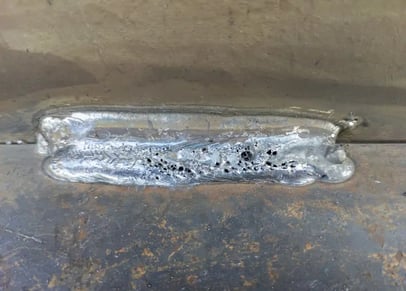
Poor protecting can result in different defects like porosity, spatter, and oxidation, jeopardizing the structural integrity of the welded joint. Sticking to proper protecting techniques is important to create high-quality welds with very little flaws and ensure the longevity and dependability of the bonded parts.
Monitoring and Control Techniques
Exactly how can welders properly monitor and manage the welding procedure to make certain optimum results and avoid problems More about the author like porosity? One secret approach is via the usage of innovative monitoring technologies. These can include real-time surveillance systems that supply responses on parameters such as voltage, current, travel rate, and gas flow rates. By continuously checking these variables, welders can identify deviations from the ideal conditions and make instant adjustments to protect against porosity formation.
In addition, carrying out appropriate training programs for welders is vital for monitoring and regulating the welding procedure properly. What is Porosity. Educating welders on the relevance of keeping constant criteria, such as appropriate gas shielding and take a trip speed, can help protect against porosity problems. Regular analyses and accreditations can also make certain that welders are competent in surveillance and managing welding processes
Moreover, using automated welding systems can boost tracking and control capacities. These systems can exactly regulate welding criteria, decreasing the chance of human error and ensuring constant weld quality. By integrating advanced tracking modern technologies, training programs, and automated systems, welders can successfully monitor and manage the welding process to lessen porosity defects and accomplish high-quality welds.
Final Thought
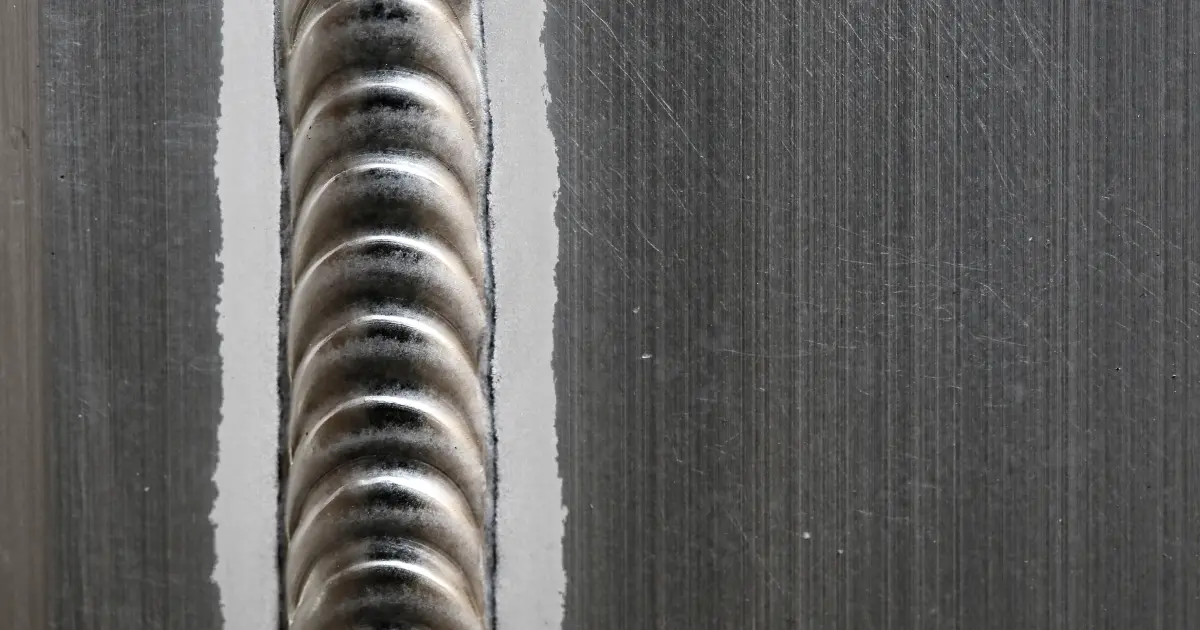
Report this wiki page